Полуавтоматичская зварювання
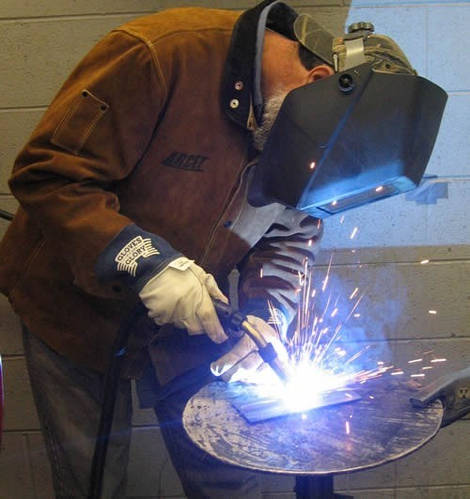
Напівавтоматичне зварювання в захисному газі
Принципи процесу, характеристики дуги
Технологічні властивості дуги істотно залежать від фізичних і хімічних властивостей захисних газів, електродного і зварюється металів, параметрів та інших умов зварювання. Це обумовлює різноманіття способів зварювання в захисних газах. Розглянемо класифікацію процесу зварювання в захисних газах плавким електродів за найбільш істотними ознаками.
Напівавтоматична зварка плавким електродом виробляється в інертних газах Аг і Не (MIG) та їх сумішах Аг + Не, в активному газі СО2 (MAG), а також у сумішах інертних і активних Аг + О2, Аг + СО2, Аг + СО + О2 і активних газів СО2 + О2. В якості електродних дротів застосовують суцільні з нелегованих і легованих сталей і кольорових металів (Ni, Си, Mg, Al, Ti, Mo), а також несуцільні порошкові і активовані. Зварювання плавким електродом виконується в основному на постійному струмі, примі змінюється також і зварювання імпульсним струмом. Знаходять застосування і інші способи зварювання: на нормальному і збільшеному вильоті, з вільним і примусовим формуванням шва, без вагань і з коливаннями електродного дроту, в атмосфері і під водою, в стандартну та нестандартну вузьку щілинну оброблення крайок і ін. Принцип дугового зварювання плавким металевим електродом в захисному газі показаний на (рис. 5).
Основні типи, конструктивні елементи і розміри зварних з'єднань сталей, а також сплавів на железоникелевой і нікелевій основах, выполняе мих дугового зварювання в захисному газі вказані в ГОСТ 14771
залежно від рівня механізації й автоматизації процесу розрізняють зварювання: — механізовану, при якій переміщення пальника виконуються вручну, а подача дроту механізована;
– автоматизовану, при якій всі переміщення пальника і подача дроту меха зированы, а керування процесом зварювання виконується оператором-зварювальником;
– автоматичну (роботизовану), при якій управління процесом зварювання виконується без безпосередньої участі оператора-зварювальника.
Зварювальне обладнання.
До складу зварювального обладнання входять джерело зварювального струму і зварювальний апарат. Складові частини зварювального обладнання та їх функції визначаються рівнем механізації і автоматизації процесу, параметрами режиму зварювання, необхідністю їх встановлення та регулювання у режимі налагодження і зварювання.
Основними параметрами автоматизованої дугового зварювання плавким електродом в СО2, Аг, і Не сумішах газів (MAG, MIG) є:
1. Зварювальний струм lc (~40., .600 А);
2. Напруга зварювання Uc (~16...4O В);
3. Швидкість зварювання Vc (~4...2О мм/с), (-14.4...72 м/год);
4. Діаметр електродного дроту dn (~0.8...2.5 мм);
5. Довжина вильоту електродного дроту Lв (~8...25 мм);
6. Швидкість подачі електродного дроту Vп (~35...25О мм/с), (-126...960 м/год);
7. Витрата захисного газу qг (~3...60 л/хв).
Принцип дугового зварювання в захисних газах визначає основні функції обладнання: — підведення до дузі електричної енергії та її регулювання (lc, Uc);
– переміщення пальника зі швидкістю зварювання (Vc) та її регулювання;
– подача електродного дроту (Vn) в зону зварювання і регулювання її швидкості;
– подача захисного газу (qг) в зону зварювання і регулювання її витрати;
– установка вильоту електродного дроту (Ц) та коригуючі переміщення пальника;
– збудження дуги і заварка кратера;
– автоматичне стеження по лінії зварювання і ін.
При пуску зварювального апарату схема управління повинна забезпечувати таку послідовність включення частин і механізмів устаткування:
1) подавання захисного газу (q р), попередню продувку системи подачі газу;
2) включення джерела живлення дуги (U);
3) подавання електродного дроту (Vэ п);
4) збудження дуги ( l, c, U c);
5) переміщення апарата зі швидкістю зварювання (Vc), тобто:
qг – > U- > Vп- > lcUc- > Vc. При закінченні зварювання послідовність вимикання механізмів повинна забезп вать заварку кратера і захист остигаючого шва:
Vc- > Vn- > lc- > Uc > U- > qг
Зварювання в захисних газах плавким електродом виконується як у виробничому приміщенні на спеціально обладнаних робочих місцях (зварювальний пост, установка, верстат, РТК) так і поза його (будівельний майданчик, траса трубопроводу та ін ). Зварювальні пости мають місцеву вентиляцію і огороджені щитами або екранами для захисту оточуючих від випромінювання дуги і бризок електродного металу.
За призначенням зварювальне обладнання поділяють на універсальне, спеціальне і спеціалізоване. Розглянемо коротко принципи компонування універсального зварювального обладнання загального призначення, що випускається серійно.
Установка для механізованого дугового зварювання плавким електродом в захисних газах зазвичай включає:
- джерело постійного струму (випрямляч);
- механізм подачі електродного дроту з касетою для дроту;
- комплект спеціальних гнучких шлангів з пальником;
- вбудований в джерело блок управління або окремий шафа управління;
- систему подачі захисного газу (балон, підігрівач газу (для СО2), газовий редуктор, змішувач газів, газові шланги, електроклапан);
- кабелі ланцюгів управління;
- зварювальні кабелі з затискачами;
- пристосування для збирання і кантовки зварного вузла (механічне обладнання).
Установка для механізованого дугового зварювання в СО2: 1 — виріб; 2 — кнопка «Пуск"–"Стоп»; 3 — пальник; 4 — гнучкий шланг; 5 — механізм подачі електродного дроту; 6 — пульт керування; 7 — котушка; 8 — кабель ланцюгів управління; 9 — блок керування напівавтоматом; 10 — шланг для подачі захисного газу; 11 — газовий редуктор; 12 — підігрівач СО2; 13 — балон з СО2; 14 — зварювальний випрямляч.
Зварювальні напівавтомати знаходять саме широке застосування, мають різне значення і конструктивне виконання. Основним виконанням напівавтоматів є за способом захисту зони дуги:
-для зварювання в активних газах (М);
-для зварювання в інертних газах (І);
-для зварювання в активних та інертних газах (У);
-для зварювання відкритою дугою (О);
-для зварювання під флюсом (Ф).
Розрізняють три основні системи подачі електродного дроту: штовхаючого, тянуще-штовхаючого і тягнучого типів. Найбільш поширеною є система подачі штовхаючого типу, яка обмежує довжину шланга (до 3 м), але відрізняється простотою і невеликою масою пальника. Інші системи дозволяють збільшити довжину шлангів до 10-20 м і використовувати тонку дріт діаметром менше 1 мм, але механізм подачі в пальнику збільшує її масу. Регулювання швидкості подачі дроту частіше застосовується плавна, але можлива плавно-ступінчасте і ступінчаста. У разі порошкового дроту застосовують дві пари подаючих роликів, щоб попередити її сплющення.
По радіусу робочої зони розрізняють напівавтомати стаціонарні (механізм подачі закріплюється на джерело зварювального струму, радіус визначається довжиною шланга), пере движные (механізм подачі можна переміщати відносно джерела до 10 м) і перенесення ві (ранцеві з довжиною кабелів до 40-50 м).
Струмопідвід (наконечник) є змінною швидко изнашиваемой деталлю. Від надій ності контакту в ньому залежить стабільність процесу зварювання.
До змінних деталей також відноситься сопло, яке нагрівається від випромінювання дуги та забризкується.
Установки для автоматизованого дугового зварювання плавким електродом в за щитных газах СО2, Аг, і Не сумішах (MAG, MIG) загального призначення зазвичай включають:
– джерело постійного або імпульсного струму;
– зварювальний апарат (трактор, підвісну або самохідну голівку) з механізмами подачі електродного дроту, переміщення зварювального апарата зі швидкістю зварювання і подъе ма-опускання пальника;
– котушку або касету зі зварювальної дротом;
– пальник з механізмом нахилу і коригувальних переміщення її по висоті і поперек шва;
– пульт управління на зварювальному апараті;
– блок управління, вбудований в зварювальний апарат або розміщений окремо шафа управління;
– систему подачі захисного газу;
– система охолодження водою.
«Інструкція з експлуатації зварювальних напівавтоматів для електрозварників. «
Зварювальні матеріали
При MIG/MAG-зварюванні використовують захисні гази та електродні дроти.
Як видно, застосовуються чисті гази інертні і активні, суміші газів в різних поєднаннях: інертні + інертні, інертні + активні та активні + активні. Водень при зварюванні плавким електродом не застосовується із-за високого разбрызгива ня. Активний газ двоокис вуглецю регламентується за ГОСТ 8050-85, кисень газоподібний за стандартом ГОСТ 5583-78.
Застосовується метод розрахунку витрати захисного газу Нг в літрах або кубічних метрах на 1 м шва визначається в основному для малого виробництва за наступною формулою:
Нр = (Нуг х Т + Ндг)
де Нг — питома витрата захисного газу, наведений в табл. 3, м3/с (л/хв); Т — основний час зварювання n-го проходу, с (хв); Ндг — додатковий витрата захисного газу на виконання підготовчо-заключних операцій при зварюванні n-го проходу.
По ГОСТ 2246-70 передбачається виготовлення 75 марок зварювальних дротів, у тому числі і для зварювання в захисних газах. Середньо - і сильноокислительные гази групи М2 і МЗ (Аг + СО2, Аг + О2, Аг + СО2 + ПРО) і С (СО, СО2 + О2) застосовуються в поєднанні з дротами, що містять раскислители Mn, Si, Al, Ti та ін (наприклад, СВ-08Г2С, СВ-08ГСМТ, СВ-08ХГ2С). Більш точні рекомендації з вибору електродних дротів доцільно давати при вивченні зварювання конкретних груп конструкційних матеріалів.
Порошкові дроти застосовуються для зварювання без захисту та з додатковим захистом зони зварювання вуглекислим газом (самозащитные і газозащитные дроту). За типом сердечника порошкові дроту можна розділити на:
1) самозащитные: рутил-органічні, карбонатно-флюоритные, флюоритные;
2) газозащитные: рутилові, рутил-флюоритные.
Застосування порошкових дротів замість суцільних дозволяє легувати шов в ши роких межах і підвищувати стійкість його проти пір і гарячих тріщин, забезпечувати за дані механічні властивості. Крім того, наявність шлаку знижує розбризкування, набризкування і покращує форму шва.
Типи переносу електродного металу і їх застосування
При зварюванні плавким електродом відкритою дугою перенесення електродного металу представляє складний процес. Багато факторів впливає на перенесення: склад і властивості захисного газу, склад і властивості електродного металу, рід струму і полярність, параметри режиму зварювання, вольт-амперна характеристика джерела струму і його динамиче ські властивості та ін.
Можна виділити наступні види переносу електродного металу:
– без коротких замикань дуги і з короткими замиканнями;
– крупно-, середньо-, мелкокапельный і струменевий;
– без розбризкування і з розбризкуванням.
Найбільш сприятливі умови для перенесення електродного металу спостерігаються при зварюванні в інертних одноатомних газах аргоні і гелії. В аргоні має місце два види міграції: крупно-крапельний без коротких замикань з невеликим розбризкуванням на докритическом струмі і струменевий на струмі більше критичного. Вид переносу впливає на форму проплавлення а) – менше критичного і б) – більше.
Зварювання зі струменевим перенесенням рекомендується на металі середньої товщини. В гелії спостерігається крапельний перенесення з короткими замиканнями (к. з. ) дуги (малі струм і напруга) і без к. з. на підвищеному струмі й напрузі при незначному дрібнокапельму розбризкуванні.
Характеристика в гелії має меншу опуклість, ніж в аргоні, так як аргон підвищує поверхневий натяг в сталях. Застосування суміші Аг+Не дозволяє використовувати переваги обох газів.
При зварюванні в СО2 мають місце перенесення мелкокапельный з к. з. і невеликим розбризкуванням, крупно-крапельний з к. з. і без к. з. з великим розбризкуванням. На великих струмах, коли дуга занурюється в основний метал, перенесення стає мелкокапельным, розбризкування зменшується, однак валик має надмірну опуклість.
Типи перенесення металу при зварюванні MIG/MAG.
При зварюванні MIG/MAG перенесення металу здійснюється, в основному, двома формами. При першій формі крапля стосується поверхні зварювальної ванни ще до відділення від торця електрода, утворюючи коротке замикання, чому цей тип перенесення отримав назву переносу з короткими замиканнями. При другій формі крапля відокремлюється від торця електрода без торкання поверхні зварювальної ванни і тому цей тип перенесення називається перенесенням без коротких замикань. Остання форма переносу металу підрозділяється на 6 окремих типів згідно особливо стям формування та відділення крапель електродного металу від торця електрода. Таким чином, згідно класифікації, запропонованої Міжнародним Інститутом Зварювання, існує 7 основних типів перенесення металу.
При перенесенні металу торець електрода з розташованої на ньому краплею розплавленого електродного металу періодично торкається поверхні зварювальної ванни, викликаючи короткі замикання і згасання дуги. Зазвичай, перенесення металу з короткими замиканнями має місце при низьких режимах зварювання, тобто, малому струмі зварювання і низькій напрузі дуги (коротка дуга гарантує, що крапля торкнеться поверх ності ванни раніше свого відділення від торця електрода). Цей тип перенесення мо талла має місце як при зварюванні MIG, так і при зварюванні MAG. На початку короткого замикання на пряжение дуги різко падає (до рівня напруги короткого замикання) і ос ється низьким до його закінчення, у той час як струм короткого замикання швид рв підвищується. Розігрів ванни рідкого металу між торцем електро так і зварювальною ванною (викликається проходять високим струмом короткого замикання) сприяє її розриву.
Перенесення металу при імпульсно-дуговому зварюванні.
Головною особливістю процесу імпульсно-дугового зварювання (ІДС) є можливість отримання дрібнокрапельне переносу електродного металу при середовищ ньому значенні струму зварювання (Ім) нижче критичного, який в звичайних умовах опрі визначає кордон між крупнокапельным і мелкокапельным перенесенням металу. У цьому методі управління перенесенням металу струм примусово з міняється між двома рівнями, званими струмом бази (Ig) і струмом імпульсу (Іі) (Рис. 9). Рівень струму бази вибирається з умови достатності для забез печення підтримки горіння дуги при незначному впливі на плавлення елек трода. Функцією струму імпульсу, який перевищує критичний струм, є вп Ілюстрація перенесення металу при ІДС (типу «одна крапля за один імпульс»).
Сталева маловуглецевої електродна дріт; 0-1,2 мм; Аг+5%02; Іі = 270 A; tu = 5,5 мс; Іб = 70 A; te = 10 мс; Vnnp = 3,5 м/хв; Vce = 28 см/хв; виліт електрода — 18 мм.
плавлення торця електрода, формування краплі певного розміру і зрив цієї краплі з торця електрода дією електромагнітної сили (Пінч-ефект). Протягом одного імпульсу струму може бути сформоване і перенесено в зварювальну ванну від однієї до декількох крапель. Частота проходження імпульсів струму, їх амплітуда та тривалість (tu) визначають виділяється енергію дуги, а слідчий але, швидкість розплавлення електрода. Сума тривалостей імпульсу tu і бази (fe) визначає період пульсації струму, а її зворотна величина дає частоту пульсації.
Перенесення електродного металу при ІДС характеризується наступними пара метрами:
– числом крапель сформованих і перейшли в зварювальну ванну під дією одного імпульсу струму;
– розміром краплі;
– часом від початку імпульсу струму до зриву першої краплі;
– моментом, коли відбувається відділення краплі від електрода (на фазі імпульсу або на фазі бази).
Аналіз параметрів пульсації струму (Iu, fa, tu, fe) і параметрів переносу елек тродного металу буде наведено нижче (див. наступну сторінку).
У зв'язку з тим, що формування і відрив краплі управляється амплітудою і тривалістю імпульсу струму (Іі і tu), середній струм зварювання (ІМ) може бути зменшений істотно нижче рівня критичного струму, що досягається або простим повели збільшенням часу бази (fe), тобто, зниженням частоти імпульсів, або зниженням струму бази (Іб). Наприклад, стосовно до маловуглецевої електродного дроту діаметром 1 мм при зварюванні в захисному середовищі на базі аргону можна підтримувати керований мелкокапельный перенесення металу на току зварювання менше 50 А, хоча критичний струм для цих умов дорівнює приблизно 180 ... 190 А. Завдяки низькій потужності дуги і швидкості розплавлення електрода, зварювальна ванна має малі розміри і легко керована. Таким чином, стає можливим реалізація бажаного дрібнокрапельне переносу електродного металу, як при зварюванні тонко листового металу, так і при зварюванні металу великої товщини у всіх пространст ських положеннях.
Іншою перевагою процесу ІДС є можливість використання дротів великих діаметрів для швидкостей наплавлення характерних для малих діаметрів дротів, що знижує вартість одиниці ваги наплавленого металу. При цьому також зростає ефективність наплавлення завдяки зниженню втрат на розбризкування електродного металу.
До недоліків цього процесу можна віднести можливе відсутність проплавлення, внаслідок низького тепловкладення в зварювальну ванну. Крім того, підвищений ві вимоги до кваліфікації зварювальників, а також використання значно бо леї складного обладнання в сукупності з більш низькою гнучкістю (універсальністю) процесу.
"ТЕХНОЛОГІЧНА ІНСТРУКЦІЯ ПО НАПІВАВТОМАТИЧНОГО ЗВАРЮВАННІ СТАЛЕЙ. « Особливості зварювання в середовищі вуглекислого газу.
Вуглекислий газ є активним газом. При високих температурах відбувається дисоціація (розкладання) його з утворенням вільного кисню:
2СО2 – > 2СО + О2
Молекулярний кисень під дією високої температуря зварювальної дуги дисоціює на атомарний за формулою:
О2 – > 2О
Атомарний кисень, будучи дуже активним, вступає в реакцію із залізом і домішками, які перебувають у стали, за наступним рівнянням:
Fe + O =FeO,
C + O =CO,
Mn + O =Mn,
Si + 2O = ЅіО2. Щоб придушить реакцію окислення вуглецю і заліза при зварюванні у вуглекислому газі, в зварювальну ванну вводять розкислювачі (марганець і кремній), які гальмують реакції окислення і відновлюють оксиди за рівнями:
FeO + Mn = Mn + Fe,
2FeO + Si = ЅіО2 + 2Fe і т. д. Утворюються оксиди кремнію і марганцю переходять в шлак. Виходячи з цього при зварюванні у вуглекислому газі маловуглецевих і низьковуглецевих сталей необхідно застосовувати кремній-марганцовистые дроту, а для зварювання легованих сталей – спеціальні дроту.
Підготовка металу під зварювання полягає в наступному. Щоб в наплавленому металі не було часу, кромки зварних з'єднань необхідно зачищати від іржі, бруду, масла і вологи на ширину до 30мм по обидві сторони від зазору. В залежності від ступеня забруднення зачищати крайки можна протиранням ганчір'ям, зачисткою сталевою щіткою, опескоструиванием, а також знежиренням з подальшим травленням. Слід зауважити, що окалина майже не впливає на якість зварного шва, тому деталі після газового різання можуть зварюватися відразу після зачистки шлаку.
Обробляють кромки під зварку так само, як і при напівавтоматичному зварюванні під шаром флюсу.
Вибір режимів зварювання в середовищі вуглекислого газу.
Режими зварювання у вуглекислому газі плавким електродом без оброблення крайок.
До параметрів режиму зварювання у вуглекислому газі належать: рід струму і полярність, діаметр електродного дроту, сила зварювального струму, напруга дуги, швидкість подачі дроту, виліт електрода, витрата вуглекислого газу, нахил електрода відносно шва і швидкість зварювання.
При зварюванні у вуглекислому газі зазвичай застосовують постійний струм зворотної полярності, так як зварювання струмом прямої полярності призводить до нестійкого горіння дуги. Змінний струм можна застосовувати тільки з осцилятором, однак у більшості випадків рекомендується застосовувати постійний струм.
Діаметр електродного дроту слід вибирати залежно від товщини зварюваного металу.
Зварювальний струм встановлюється в залежності від обраного діаметра електродного дроту.
Основні режими зварювання напівавтоматом.
Із збільшенням сили зварювального струму збільшується глибина провару і підвищується продуктивність процесу зварювання.
Напруга дуги залежить від довжини дуги. Чим довше дуга, тим більше напруги на ній. Із збільшенням напруги дуги збільшується ширина шва зменшується глибина його провару. Встановлюється напруга дуги в залежності від обраної сили зварювального струму.
Швидкість подачі електродного дроту підбирають з таким розрахунком, щоб забезпечувалося стійке горіння дуги при вибраному напрузі на ній.
Вильотом електрода називається довжина відрізка електрода між його кінцем і виходом його з мундштука. Величина вильоту надає великий вплив на стійкість процесу зварювання і якості зварного шва. Із збільшенням вильоту погіршується стійкість горіння дуги і формування шва, а також збільшується розбризкування. При зварюванні з дуже малим вильотом може спостереження за процесом зварювання і часто підгорає контактний наконечник. Величину вильоту рекомендується вибирати залежно від діаметра електродного дроту.
Крім вильоту електрода, необхідно витримувати певну відстань від сопла пальника до виробу, так як із збільшенням цієї відстані можливе потрапляння кисню та азоту повітря в наплавлений метал і утворення пір в шві. Величину відстані від сопла пальника до виробу слід витримувати в певних значеннях.
Витрата вуглекислого газу визначають у залежності від сили струму, швидкості зварювання, типу з'єднання і вильоту електрода. У середньому газу витрачається від 5 до 20 л/хв.
Нахил електрода відносно шва має великий вплив на глибину провару і якість шва. В залежності від кута нахилу зварювання можна проводити кутом назад і кутом вперед.
При зварюванні кутом назад в межах 5 – 10 град. поліпшується видимість зони зварювання, підвищується глибина провару і наплавлений метал виходить більш щільним.
При зварюванні кутом вперед важче спостерігати за формуванням шва, але краще спостерігати за зварюваними кромками і направляти електрод точно по щілинах. Ширина валика при цьому зростає, а глибина провару зменшується. Цей спосіб рекомендується застосовувати при зварюванні тонкого металу, де існує небезпека наскрізного пропалення.
Швидкість зварювання встановлюється самим зварником в залежності від товщини металу та необхідної площі поперечного перерізу шва. При занадто великій швидкості зварювання кінець електрода може вийти з-під зони захисту газом і окислюватися на повітрі.
Основні вимоги безпеки праці при напівавтоматичного зварюванні. 1. Перед пуском зварювального напівавтомата необхідно перевірити справність пускового пристрою (рубильника, кнопкового вимикача).
2. Корпуса джерела живлення дуги і апаратного ящика повинні бути заземлені.
3. При включенні напівавтомата спочатку слід включити рубильник ( магнітний пускач), а потім – апаратний ящик. При вимиканні – навпаки.
4. Шланги для захисного газу і водяного охолодження у напівавтомата в місцях з'єднання зі штуцерами не повинні пропускати газ і воду.
5. Опиратися або сідати на джерело живлення дуги і апаратний ящик забороняється.
6. При роботі відкритою дугою на відстані менше 10м необхідно огороджувати місця зварювання або користуватися захисними окулярами.
7. Намотування зварювального дроту з бухти на касету слід виробляти лише після спеціального інструктажу.
8. По закінченні роботи вимкнути струм, газ, воду.
9. Про помічені несправності в роботі обладнання необхідно доповісти майстру цеху і без його вказівки до роботи не приступати.
10. Усувати несправності напівавтоматах самому зварнику забороняється.